What is Push Compensation in Embroidery Digitizing?
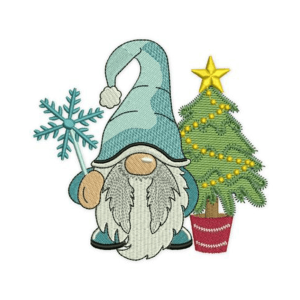
Embroidery digitizing is a complex art that combines creativity and technical precision. One of its most critical aspects is push compensation, an adjustment that ensures designs appear flawless when stitched onto fabric. Push compensation addresses distortions caused by the natural stretching of stitches, helping embroidery maintain its intended shape and proportions. If you’re looking to enhance your skills in digitize for embroidery, understanding push compensation is essential.
Understanding Push Compensation
What is Push Distortion?
Push distortion occurs when embroidery stitches naturally stretch fabric outward during stitching. This causes designs to elongate or shift, particularly at the ends of filled or satin-stitched areas.
For example:
- A rectangle might appear longer than designed due to push distortion.
- Circular shapes may become ovals, distorting the intended design.
Why is Push Compensation Important?
Push compensation counters these distortions, ensuring that the final embroidered design matches the original digital file. By anticipating and adjusting for push distortion, digitizers can:
- Achieve accurate shapes.
- Prevent elements from overlapping or misaligning.
- Maintain professional-quality embroidery results.
How Push Compensation Works in Embroidery Digitizing
1. Adjusting Stitch Length
EMB digitizing software allows you to reduce or extend stitch lengths at critical points in the design. This preemptively corrects areas prone to distortion.
2. Adding Overlap
For areas where elements meet, such as text or borders, slight overlaps are added to prevent gaps caused by fabric stretch.
3. Modifying Stitch Angles
Altering stitch angles in certain sections helps distribute tension evenly, reducing the risk of distortion.
Types of Push Compensation Techniques
1. Manual Push Compensation
Involves manually adjusting stitch placement and density using embroidery software. While time-consuming, it offers the highest level of control and precision.
2. Automatic Push Compensation
Modern embroidery software like Wilcom or Hatch includes built-in tools to calculate and apply push compensation automatically. This saves time but may require fine-tuning for complex designs.
3. Fabric-Specific Adjustments
Different fabrics react uniquely to embroidery. For instance:
- Stretchy fabrics like jersey need more compensation.
- Stiffer materials like canvas require minimal adjustments.
Factors Influencing Push Distortion
1. Fabric Type
Stretchy or lightweight fabrics are more prone to distortion compared to thicker, stable materials.
2. Stitch Type
- Satin Stitches: More likely to stretch and cause distortion due to their length.
- Fill Stitches: Typically more stable but can still push outward at the edges.
3. Stitch Density
Higher stitch density increases tension on the fabric, leading to more distortion.
4. Design Complexity
Intricate or closely packed designs are more susceptible to push distortion, requiring careful compensation.
Step-by-Step Guide to Applying Push Compensation
Step 1: Analyze the Design
Identify areas prone to push distortion, such as long satin stitches or elements that meet at sharp angles.
Step 2: Adjust Stitch Placement
- Use your embroidery software to extend or shorten stitches at the edges.
- Add overlaps where different design elements meet.
Step 3: Test on Similar Fabric
Stitch a sample on the fabric type you’ll be using. Observe distortions and refine your push compensation settings accordingly.
Step 4: Refine Using Feedback
Evaluate the stitched sample and make further adjustments until the design appears flawless.
Common Mistakes in Push Compensation
1. Overcompensation
Adding too much push compensation can lead to overlapping or uneven stitches, ruining the design’s appearance.
2. Ignoring Fabric Behavior
Failing to account for the fabric’s unique properties can result in inadequate or excessive compensation.
3. Relying Solely on Automatic Settings
While automatic tools are helpful, they may not account for all nuances in the design. Manual adjustments are often necessary.
Tools for Push Compensation
1. Professional Embroidery Software
- Wilcom Hatch: Offers advanced tools for manual and automatic push compensation.
- Brother PE-Design: Includes fabric-specific settings to optimize compensation.
2. Test Hoops
Testing your design on similar fabric ensures accurate adjustments.
3. Stabilizers
Using proper backing stabilizers minimizes fabric movement, reducing the need for extreme compensation.
Conclusion
Mastering push compensation is a cornerstone of professional embroidery digitizing. It ensures that designs remain accurate, visually appealing, and free from distortions. Whether you’re a beginner learning to digitize for embroidery or an experienced professional refining your craft, understanding push compensation will elevate the quality of your work. By combining the right techniques, tools, and practice, you can achieve flawless embroidery results on any fabric.
FAQs About Push Compensation in Embroidery Digitizing
1. What is push compensation in simple terms?
Push compensation involves adjusting embroidery designs to counteract distortions caused by fabric stretching during stitching.
2. Do all designs require push compensation?
Yes, especially designs with long satin stitches or those intended for stretchy fabrics.
3. Can I use automatic push compensation tools?
Yes, most modern embroidery software includes automatic settings, but manual adjustments may still be needed for complex designs.
4. How do I know if I’ve applied enough push compensation?
Stitch a sample design on the intended fabric and evaluate its accuracy. Adjust as needed.
5. Can push compensation fix gaps in embroidery?
Yes, by adding overlaps and adjusting stitch placement, push compensation can prevent gaps caused by fabric distortion.
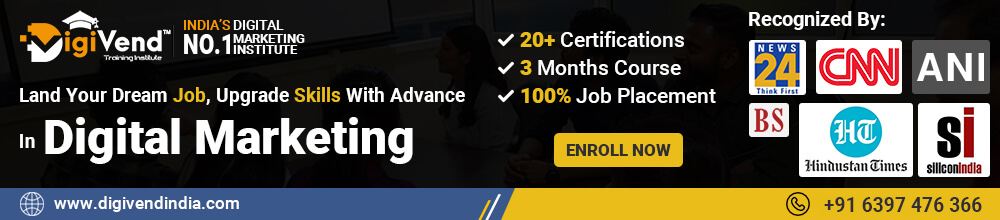