Unleashing the Power of Flux Welders: A Comprehensive Guide
Introduction:
Flux welders are transforming the welding landscape with their versatility and efficiency. In this comprehensive guide. we delve deep into the world of flux welders, exploring their functionality, applications, benefits. Key considerations for choosing the right one for your welding needs.
What is a Flux Welder?
Understanding the fundamentals of flux welders is crucial for harnessing their potential. A flux welder, also known as a flux-core welder, utilizes a continuous electrode wire with a flux core, eliminating the need for external shielding gas. This innovative design makes flux welders highly portable and ideal for outdoor welding tasks.
How Flux Welders Work:
Delving into the inner workings of flux welders unveils their ingenious mechanism. During the welding process, the flux core melts and releases a shielding gas. Protects the weld pool from atmospheric contaminants. This self-shielding feature enables flux welders to produce strong and clean welds even in windy or adverse conditions.
Applications of Flux Welders:
Flux welders are renowned for their versatility, catering to a wide range of welding applications across various industries. From automotive repairs and construction projects to shipbuilding and pipeline welding, flux welders excel in providing robust and durable welds on ferrous metals like steel and iron.
Advantages of Flux Welders:
- Portability: With their self-shielding mechanism, flux welders offer unmatched portability, making them indispensable for on-site welding tasks.
- Cost-Effectiveness: Eliminating the need for external shielding gas reduces operational costs, making flux welders a budget-friendly option for both professionals and hobbyists.
- Versatility: Flux welders can weld thicker materials than traditional MIG welders, offering greater versatility in handling a variety of welding projects.
- Ease of Use: The simplicity of flux welders, coupled with their forgiving nature, makes them suitable for welders of all skill levels, from beginners to seasoned professionals.
Choosing the Right Flux Welder:
When selecting a flux welder, several factors warrant consideration to ensure optimal performance and compatibility with your welding requirements. Key factors include:
- Power Output: Determine the appropriate power output based on the thickness of the materials you intend to weld.
- Duty Cycle: Consider the duty cycle, which indicates the percentage of time a welder can operate continuously without overheating.
- Wire Feed Speed Control: Opt for a flux welder with adjustable wire feed speed control for precise welding performance.
- Portability Features: Assess the weight and dimensions of the flux welder, especially if you anticipate frequent transportation to different job sites.
- Brand Reputation and Warranty: Choose reputable brands known for their quality craftsmanship and reliability, backed by comprehensive warranty coverage for peace of mind.
Maintenance Tips for Flux Welders:
Proper maintenance is essential to prolong the lifespan and ensure consistent performance of flux welders. Follow these maintenance tips:
- Clean the Welding Gun: Regularly clean the welding gun and replace worn-out consumables to maintain optimal welding performance.
- Inspect the Ground Clamp: Ensure the ground clamp makes secure contact with the workpiece to prevent erratic welding behavior.
- Check for Wire Jamming: Periodically inspect the wire feeder mechanism for any signs of wire jamming or irregular feeding.
- Monitor Gas Flow: If using a gas shielded flux welder, monitor gas flow to ensure adequate shielding during the welding process.
- Keep the Welding Environment Clean: Minimize debris and contaminants in the welding environment to prevent interference with the welding process.
Conclusion:
Flux welders represent a paradigm shift in welding technology, offering unmatched versatility, portability, and cost-effectiveness. By understanding their functionality, applications, and maintenance requirements, Welders can harness the full potential of flux welders to tackle diverse welding projects with precision and efficiency. A flux welder is a versatile tool that can be used for a wide range of welding projects. Its ease of use and ability to produce clean and strong welds make it a valuable addition to any workshop. With a flux welder, you can tackle various welding tasks with confidence and precision, making your projects more efficient and professional-looking.
Remember, when it comes to flux welders, the possibilities are limitless – ignite your creativity and weld with confidence! Delving into the inner workings of flux welders unveils their ingenious mechanism. During the welding process, the flux core melts and releases a shielding gas that protects the weld pool from atmospheric contaminants. This self-shielding feature enables flux welders to produce strong and clean welds even in windy or adverse conditions.
Flux welders are transforming the welding landscape with their versatility and efficiency. In this comprehensive guide, we delve deep into the world of flux welders, exploring their functionality, applications, benefits, and key considerations for choosing the right one for your welding needs.
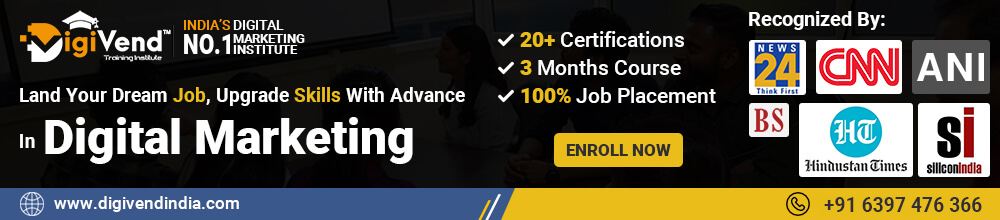