Unraveling the Mystery: How Many Screws in Drywall?

Introduction:
When it comes to hanging drywall, one of the most common questions that DIY enthusiasts and professionals alike ponder is: How many screws do I need? The answer to this seemingly simple question is influenced by various factors, including the size of the drywall sheets, the spacing between the screws, and the type of project at hand. In this comprehensive guide, we’ll delve into the intricacies of estimating the number of screws required for your drywall project, ensuring a sturdy and visually appealing finish.
Before delving into the specifics of screw quantity, it’s essential to recognize the importance of accurate estimation in the realm of drywall installation. Professional Drywall Estimating Services play a crucial role in ensuring that projects are planned meticulously, materials are efficiently utilized, and costs are kept within budgetary constraints. These services employ a combination of industry expertise, technological tools, and precise measurements to provide clients with detailed estimates tailored to their unique requirements. Whether it’s a residential renovation or a commercial construction endeavor, relying on professional estimators can streamline the planning process and minimize the risk of material shortages or excess.
Factors Influencing Screw Quantity:
Determining the number of screws needed for a drywall installation involves considering several key factors. Firstly, the size and thickness of the drywall sheets significantly impact screw placement. Thicker sheets may require more screws to provide adequate support and prevent sagging over time. Additionally, the spacing between screws plays a crucial role in achieving structural integrity and preventing surface imperfections such as bulges or cracks. While standard practice often dictates placing screws every 12 inches along the perimeter and every 16 inches in the field, variations may occur based on specific project requirements or building codes.
Moreover, the type of framing material and the intended use of the space can influence screw quantity. For instance, attaching drywall to metal studs may necessitate different spacing and fastening techniques compared to wood framing. Similarly, areas subject to high humidity or frequent impact, such as bathrooms or utility rooms, may require additional screws to enhance durability and resilience.
Calculating Screw Quantity:
To calculate the approximate number of screws required for a drywall installation, a systematic approach is essential. Begin by measuring the surface area to be covered by drywall, taking into account any openings for doors, windows, or fixtures. Next, determine the desired spacing between screws based on industry standards or project-specific requirements. Utilizing these measurements, multiply the total square footage by the recommended screw spacing to obtain a preliminary estimate.
However, it’s important to account for factors that may increase screw quantity, such as irregularities in the wall surface, the presence of corner beads or edging, and any specialized framing configurations. Additionally, it’s advisable to include a buffer of extra screws to accommodate unforeseen challenges or adjustments during the installation process.
Fine-Tuning the Estimate:
While mathematical calculations provide a baseline for screw quantity, experienced professionals often rely on practical knowledge and on-site assessments to refine their estimates. Factors such as the condition of the framing, accessibility of the installation area, and the skill level of the workforce can influence the actual number of screws needed. Therefore, periodic reassessment and adjustment of the estimate based on real-time observations are crucial for optimizing resource allocation and project efficiency.
Exploring Alternative Approaches:
In the realm of drywall installation, there are alternative approaches to traditional screw fastening methods that may influence the overall quantity of screws required. For instance, some professionals opt for adhesive-backed drywall, which eliminates the need for screws in certain applications. While this technique offers advantages such as faster installation and reduced risk of screw pops, it requires careful surface preparation and may not be suitable for all projects. Additionally, innovative fastening systems, such as self-drilling drywall anchors or magnetic attachment systems, present viable alternatives that can streamline the installation process and enhance flexibility.
Addressing Specialized Requirements:
Certain scenarios demand specialized considerations when estimating screw quantity for drywall installation. In seismic zones or areas prone to high winds, building codes may mandate enhanced fastening requirements to ensure structural resilience and mitigate the risk of damage during natural disasters. Similarly, acoustic or fire-rated assemblies may necessitate specific screw spacing and materials to maintain compliance with regulatory standards and achieve desired performance characteristics. By consulting industry guidelines and collaborating with relevant stakeholders, such as architects, engineers, and regulatory authorities, contractors can tailor their screw quantity estimates to meet the unique requirements of each project.
Embracing Technological Advancements:
In recent years, advancements in technology have revolutionized the field of drywall estimating, offering innovative solutions to streamline the estimation process and enhance accuracy. Digital tools, such as building information modeling (BIM) software and estimating applications, enable contractors to generate detailed 3D models, visualize project scopes, and precisely calculate material quantities, including screws. These digital resources not only expedite the estimation process but also facilitate seamless collaboration among project stakeholders, leading to improved project outcomes and client satisfaction.
Continual Improvement and Adaptation:
As the construction industry evolves and new techniques emerge, professionals involved in drywall installation need to embrace a mindset of continual improvement and adaptation. By staying abreast of industry trends, attending training programs, and actively seeking feedback from peers and clients, contractors can refine their estimating practices, optimize resource utilization, and deliver superior results. Ultimately, by fostering a culture of innovation and knowledge sharing within the industry, stakeholders can collectively elevate standards of quality and efficiency in drywall installation practices.
To read more articles visit Hit Upon Views
Conclusion:
In navigating the intricacies of estimating screw quantity for drywall installation, it’s evident that multiple factors come into play, from technological advancements to specialized requirements and alternative approaches. By leveraging a combination of technical expertise, practical judgment, and collaborative engagement, professionals can refine their estimating processes, enhance project outcomes, and ultimately contribute to the advancement of the construction industry as a whole. With a proactive mindset and a commitment to excellence, every screw placed in drywall becomes not just a fastener, but a testament to precision, professionalism, and craftsmanship.
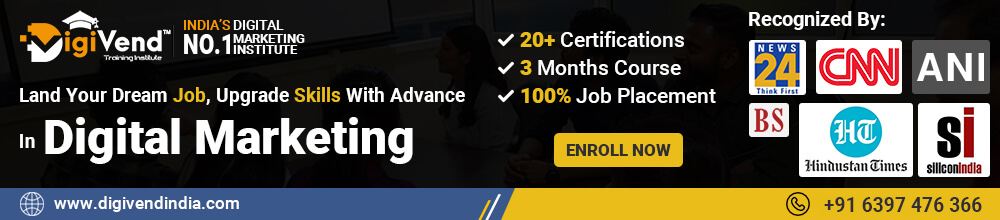