The Environmental Impact of Choosing Closed-Cell Spray Foam
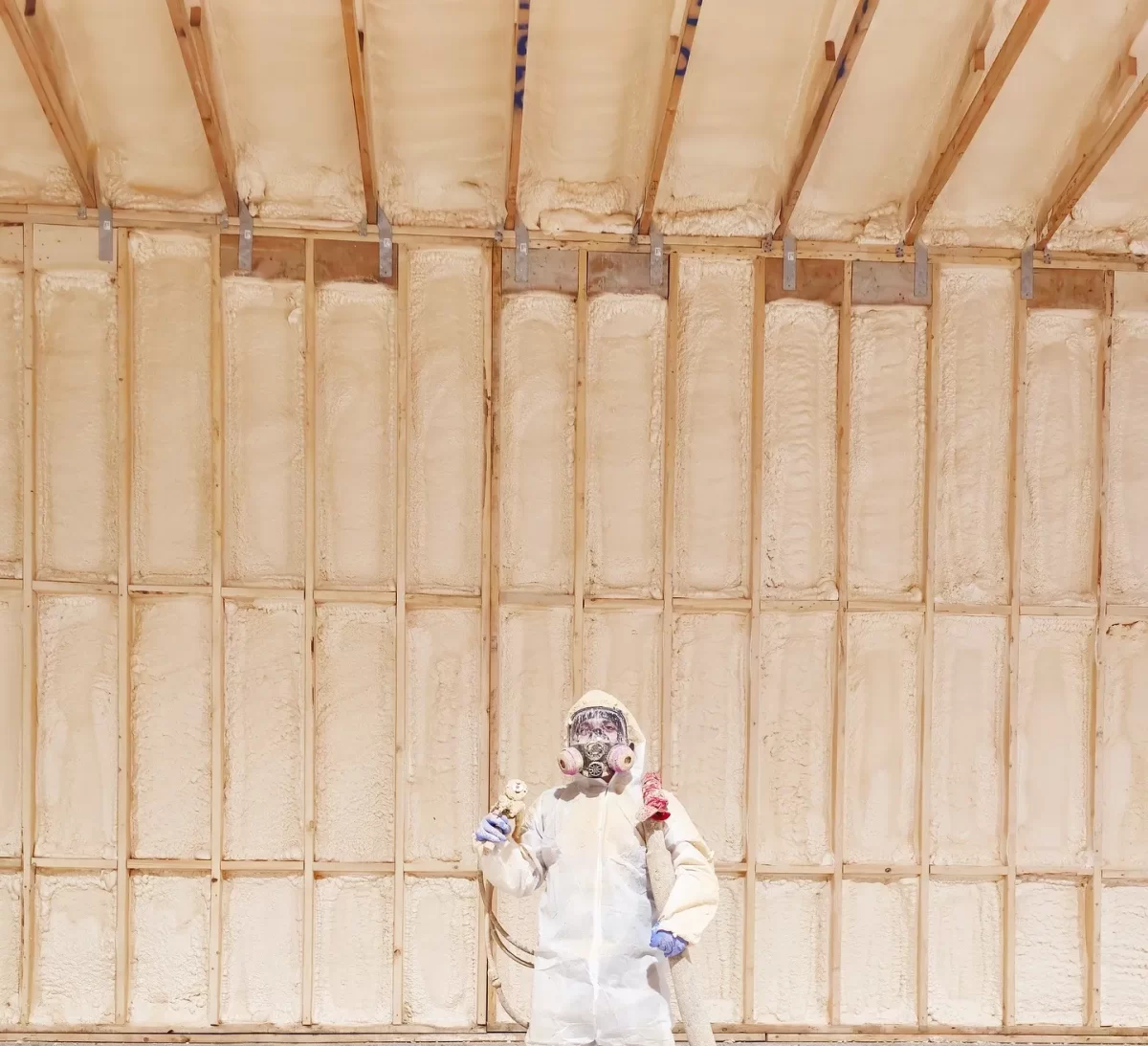
Closed-cell spray foam insulation provides superior thermal resistance and effective air sealing, but it also poses significant environmental trade-offs. While it can reduce building energy consumption by up to 50%, its production process depends on fossil fuels, generates volatile organic compounds (VOCs), and often uses high-global-warming-potential (GWP) blowing agents. This dual nature—high efficiency versus high embodied emissions—makes it a complex choice from an environmental standpoint.
This article investigates the comprehensive environmental impact of closed-cell spray foam insulation, offering detailed technical data, real-world comparisons, and lifecycle considerations. It presents an unbiased resource for homeowners, builders, and sustainability-minded decision-makers to evaluate the implications of this insulation choice.
How Closed-Cell Spray Foam Affects the Environment
Closed-cell spray foam’s dense, rigid structure results in excellent thermal resistance and water resistance. These properties significantly reduce heating and cooling loads in buildings, contributing to lower operational carbon emissions. Yet, the environmental burden of manufacturing and disposal can offset these gains if not considered holistically.
Key Environmental Factors:
- Energy Efficiency Gains: Closed-cell foam reduces energy demand, cutting heating/cooling emissions.
- Petrochemical Base: Ingredients include polyurethane and polyisocyanurate, derived from fossil fuels.
- High-GWP Blowing Agents: Older versions use HFCs with GWP values over 1,000.
- End-of-Life Disposal: Non-biodegradable and rarely recycled, contributing to long-term landfill volume.
- Off-Gassing Risk: Emits VOCs during application, posing short-term indoor air quality concerns.
Technical Data and Environmental Metrics
Specification | Closed-Cell Spray Foam |
R-Value per Inch | 6.0 to 7.0 |
Global Warming Potential (HFC-based) | ~1000–1400 GWP units |
Global Warming Potential (HFO-based) | ~1 |
VOC Emissions (During Curing) | Moderate to High |
Water Resistance | Excellent |
Air Seal Effectiveness | High |
Bio-based Content | Typically <5% |
Recyclability | Low |
Lifespan | 50+ years |
Embodied Carbon (avg per m^2) | ~15–25 kg CO2-eq |
Comparison With Other Insulation Types
Feature | Closed-Cell Spray Foam | Open-Cell Spray Foam | Fiberglass | Cellulose |
R-Value per Inch | 6.0–7.0 | 3.5–4.0 | 2.9–3.8 | 3.2–3.8 |
Water Resistance | Excellent | Poor | Poor | Poor |
Air Barrier | Yes | Yes | No | No |
GWP (typical) | High (HFC: 1000+) | Medium | Low | Low |
Recyclability | Low | Low | Medium | High |
Bio-Based Content | <5% | <5% | None | 85–100% |
Installation Health Risk | Moderate | Moderate | Low | Low |
Fire Resistance | High | Moderate | Moderate | Low |
Settling Risk Over Time | None | Minimal | Moderate | High |
Lifecycle and Emission Reduction Potential
Although its initial carbon footprint is high, closed-cell spray foam can yield significant lifecycle emission reductions through decades of energy savings. In cold or hot climates where HVAC usage is intensive, its insulation efficiency translates directly to lower fossil fuel consumption.
Bonus Tip: In retrofits or deep energy remodels, combining closed-cell foam with natural fiber boards or other low-carbon sheathing materials can balance emissions and enhance sustainability.
Things to Consider Before Making a Decision
- Climate Zone: Closed-cell foam performs best in extreme climates requiring robust thermal resistance.
- Moisture Risk: Ideal in basements, crawlspaces, and coastal/flood-prone areas due to water impermeability.
- Building Longevity: Long product life helps offset initial emissions if structure lifespan exceeds 30–50 years.
- Air Quality During Install: Requires protective measures due to isocyanate exposure risks.
- Retrofitting Constraints: Expands rapidly and can distort wall assemblies in poorly planned retrofits.
- Cost vs. Performance: Higher upfront cost may be justified by long-term energy and moisture control benefits.
- Third-Party Certifications: Seek GREENGUARD Gold or products meeting LEED v4 criteria.
Bonus Tip: Request documentation on the type of blowing agent used—HFO-based agents offer near-zero GWP and perform comparably.
Common Questions About Environmental Impact
Is closed-cell spray foam environmentally friendly?
It’s relatively efficient in operation but high-impact in production. The balance depends on climate, building type, and lifespan.
Can it be recycled or reused?
There are currently no scalable recycling methods. It must be landfilled or incinerated at end of life.
How long does it take to offset its embodied emissions?
In colder climates, typical ROI in carbon terms is 3–5 years. In mild zones, payback periods may extend beyond a decade.
Are safer, lower-emission variants available?
Yes. HFO-based foams provide similar performance with 99.9% lower GWP than HFC-based predecessors.
What should I avoid when selecting a spray foam product?
Avoid outdated HFC-based products, uncertified brands, or contractors that lack training in ventilation and curing practices.
Closed-Cell Spray Foam FAQ
What is the main environmental concern with closed-cell spray foam?
Its chemical ingredients and use of high-GWP blowing agents create a substantial carbon footprint during manufacturing.
Does it off-gas harmful substances long-term?
No, the majority of emissions occur during installation. After curing, it is relatively inert unless disturbed.
Can I combine it with other insulation to reduce impact?
Yes. Hybrid systems using smaller amounts of closed-cell foam with natural insulation can lower embodied carbon.
How long does it typically last?
50+ years with minimal degradation. It contributes to overall building durability and structural strength.
How do I ensure it aligns with green building goals?
Verify low-GWP blowing agent use, request manufacturer disclosures, and use qualified installers.
Make the Right Decision
Closed-cell spray foam insulation services deliver unparalleled air sealing and moisture control performance, but its environmental footprint depends on the formulation, application method, and overall building strategy. Prioritize lower-impact materials like HFO-blown variants and combine them with sustainable design practices.
Assess your project’s climate zone, indoor air quality concerns, and lifecycle goals before committing. With informed choices, closed-cell spray foam can be a viable component in a responsible building strategy.
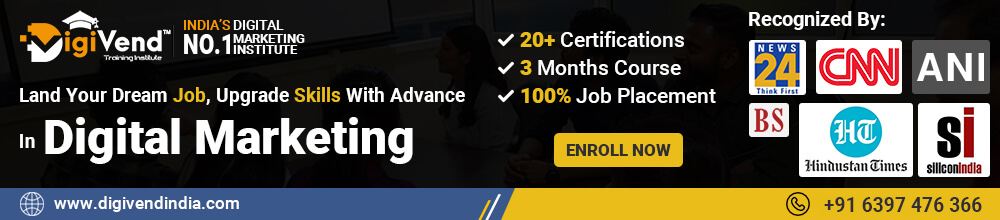