The Complete Guide to Warehouse Mapping: Optimizing Space, Efficiency, and Safety

Introduction to Warehouse Mapping
In today’s fast-paced logistics and supply chain environment, warehouse mapping has emerged as a critical tool for businesses looking to maximize efficiency, reduce operational costs, and improve safety. Warehouse mapping involves creating detailed digital or physical representations of a warehouse’s layout, inventory locations, and workflow processes. This strategic approach helps businesses visualize their operations, identify bottlenecks, and implement data-driven improvements.
With the rise of e-commerce and just-in-time inventory systems, the need for precise warehouse organization has never been greater. Studies show that companies implementing warehouse mapping solutions can reduce picking errors by up to 67% and improve space utilization by 30%. Whether you’re managing a small distribution center or a massive fulfillment warehouse, proper mapping techniques can transform your operations.
Why Warehouse Mapping Matters
1. Maximizing Storage Space Utilization
One of the primary benefits of warehouse mapping is optimizing available space. By analyzing your current layout through mapping, you can:
- Identify underutilized vertical space
- Reorganize storage zones based on product velocity
- Implement high-density storage solutions like mezzanines or narrow-aisle racking
2. Improving Picking Efficiency
Order picking accounts for nearly 55% of warehouse operating costs. Effective warehouse mapping helps:
- Create optimal pick paths to reduce travel time
- Implement zone or wave picking strategies
- Position fast-moving items in easily accessible locations
3. Enhancing Safety and Compliance
A well-mapped warehouse significantly reduces workplace accidents by:
- Clearly marking hazardous material storage areas
- Defining proper aisle widths for equipment movement
- Identifying emergency exit routes and safety zones
4. Supporting Automation and Technology Integration
Modern warehouses increasingly rely on automation. Warehouse mapping provides the foundation for:
- Automated storage and retrieval systems (AS/RS)
- Autonomous mobile robots (AMRs)
- Warehouse management system (WMS) integration
Types of Warehouse Mapping
1. 2D Layout Mapping
The most basic form uses CAD or simple diagramming tools to create:
- Floor plan visualizations
- Racking and storage locations
- Traffic flow patterns
2. 3D Warehouse Modeling
Advanced solutions offer:
- Photorealistic renderings of the entire facility
- Virtual walkthroughs for planning changes
- Space utilization heat maps
3. Digital Twin Technology
The cutting edge of warehouse mapping creates virtual replicas that:
- Simulate operational scenarios
- Test layout changes before implementation
- Integrate real-time IoT sensor data
4. RFID and Barcode Mapping
Combines physical mapping with:
- Real-time inventory tracking
- Automated location updates
- Dynamic routing optimization
Key Steps in Warehouse Mapping Process
1. Data Collection and Assessment
- Conduct physical measurements of the facility
- Document current storage systems and equipment
- Analyze inventory profiles and turnover rates
2. Zone Identification and Segmentation
- Define receiving, storage, picking, packing, and shipping areas
- Establish temperature-controlled zones if needed
- Create dedicated spaces for returns processing
3. Inventory Slotting Optimization
- Classify items by size, weight, and turnover frequency
- Implement ABC analysis for strategic placement
- Consider special requirements (hazardous materials, etc.)
4. Workflow Analysis and Path Optimization
- Map current employee and equipment movement
- Identify congestion points and bottlenecks
- Design efficient travel routes
5. Technology Integration
- Select appropriate WMS software
- Implement barcode or RFID systems
- Consider automation compatibility
Advanced Warehouse Mapping Technologies
1. Warehouse Management Systems (WMS)
Modern WMS solutions offer:
- Real-time inventory visibility
- Automated replenishment triggers
- Intelligent picking algorithms
2. Indoor Positioning Systems (IPS)
Using technologies like:
- Bluetooth beacons
- Ultra-wideband (UWB)
- RFID triangulation
3. Augmented Reality (AR) for Warehousing
Emerging AR applications include:
- Visual pick-path guidance
- Hands-free inventory management
- Equipment maintenance overlays
4. Drones for Warehouse Mapping
Aerial drones provide:
- Rapid facility surveys
- Hard-to-reach area inspections
- Inventory audits
Best Practices for Effective Warehouse Mapping
- Start with Accurate Measurements – Ensure all dimensions are precise for reliable planning
- Involve Cross-Functional Teams – Include operations, safety, and IT perspectives
- Consider Future Growth – Design flexible layouts that can scale with business needs
- Regularly Update Maps – Maintain current representations as operations evolve
- Train Staff on New Systems – Ensure team members understand and utilize mapping tools
Common Warehouse Mapping Mistakes to Avoid
- Overlooking Vertical Space – Failing to utilize the full cube of the facility
- Static Mapping – Not updating layouts as inventory profiles change
- Ignoring Workflow Patterns – Designing based on space alone rather than operational flow
- Poor Technology Integration – Choosing mapping solutions that don’t sync with existing systems
- Insufficient Safety Considerations – Not accounting for emergency access and equipment clearances
The Future of Warehouse Mapping
As technology advances, warehouse mapping is evolving with:
- AI-powered layout optimization – Machine learning algorithms that continuously improve space utilization
- Real-time dynamic mapping – Systems that automatically adjust to inventory and workflow changes
- Integration with smart glasses – AR interfaces that overlay mapping data directly in workers’ field of view
- Predictive analytics – Forecasting future space needs based on sales trends and seasonality
Conclusion
Effective warehouse mapping is no longer optional for competitive logistics operations. It serves as the foundation for efficient space utilization, optimized workflows, and seamless technology integration. By implementing comprehensive mapping strategies, businesses can achieve significant improvements in productivity, accuracy, and safety.
As warehouse operations grow increasingly complex, the companies that invest in advanced mapping solutions will gain a strategic advantage. Whether you’re just starting with basic 2D layouts or ready to implement digital twin technology, now is the time to evaluate your warehouse mapping approach.
Ready to transform your warehouse operations? Begin with a thorough mapping assessment to identify your biggest opportunities for improvement. The ROI in terms of space savings, labor efficiency, and error reduction will quickly justify the investment.
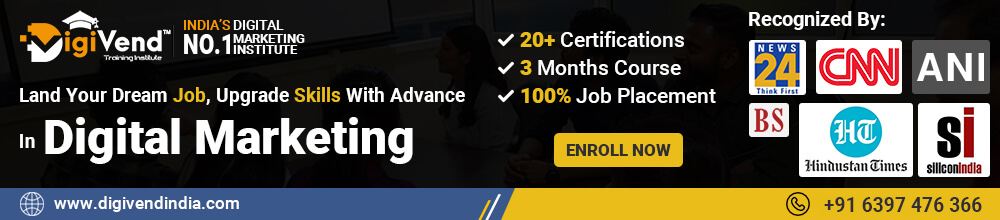