ISO 9001: Your Path to Continuous Improvement and Long-Term Success
It’s no secret that every business wants to improve. But how many organizations truly know how to put continuous improvement into action? If you’re aiming for growth, better quality, and a more efficient operation, ISO 9001 might be the framework you’ve been searching for.
This certification isn’t just another fancy title for your company’s wall. It’s a mindset—one that puts quality at the forefront of your organization’s culture. It’s about ensuring every product, every service, and every customer interaction is the best it can possibly be. And it’s about ensuring that your business keeps getting better over time, with no plateau in sight.
But what does ISO 9001 actually mean for your company? And how can it help you build a culture of continuous improvement? Let’s walk through it together.
What Exactly Is ISO 9001?
At its core, ISO 9001 is a set of standards for a Quality Management System (QMS). Think of it as a blueprint for how your company can consistently deliver products and services that meet or exceed customer expectations.
ISO 9001 isn’t just a set of rules—it’s a philosophy that encourages businesses to take a structured approach to quality management. It’s about establishing systems and processes that help improve the way you operate, and it’s designed to be applicable to any industry, no matter the size or scale.
Here’s the kicker: it doesn’t stop once you’re certified. ISO 9001 is all about continuous improvement—always seeking better ways to do things, streamline operations, and ensure that your products and services consistently align with what your customers want. It’s about making sure that quality isn’t a one-off; it’s built into your organization’s DNA.
Why Should Your Business Pursue ISO 9001 Certification?
You might be thinking, “Why should I bother with this certification? What’s in it for me?” Well, let’s break it down:
1. Better Efficiency Across the Board
Implementing ISO 9001 forces you to take a hard look at your processes. It encourages businesses to identify areas where they can streamline, reduce waste, and improve workflow. So, you’re not just looking at the big picture; you’re zooming in on those everyday practices that can make a huge difference. Over time, this leads to better efficiency—and that means more productivity and less downtime.
2. Improved Customer Satisfaction
Here’s the thing: when you’re focused on quality, your customers notice. ISO 9001 helps ensure that you’re meeting customer expectations, which builds trust and loyalty. The better your processes, the better your outcomes. When customers are happy, they return, and they tell others about their positive experiences. It’s a win-win.
3. Competitive Edge in the Market
Think about it—having ISO 9001 on your resume is like wearing a badge of honor. It signals to your customers, partners, and stakeholders that your company is committed to quality and continuous improvement. In a crowded market, that can give you a huge edge over competitors who aren’t certified. It says, “We don’t just meet the minimum; we exceed expectations.”
4. Clearer Processes and Structure
Implementing ISO 9001 forces you to define your processes clearly. You have to establish documented procedures, identify roles, and outline expectations. While that might seem like extra paperwork, it’s actually a huge advantage. Why? Because clear, well-documented processes help reduce confusion, miscommunication, and errors. Plus, when everyone knows their role and expectations, your company runs like a well-oiled machine.
The Steps to Achieving ISO 9001 Certification
Achieving ISO 9001 certification is a significant undertaking, but it’s entirely doable with the right steps. Here’s what the process generally looks like:
1. Get Leadership Buy-In
ISO 9001 doesn’t work unless everyone’s on board, especially the leadership team. It starts at the top. Management needs to be actively involved, both in the planning and the execution of the process. After all, they’re the ones who set the tone for the rest of the company.
2. Define Your Quality Management System (QMS)
The next step is to define what your Quality Management System (QMS) looks like. This system will guide everything you do when it comes to quality management. It’s about developing a structure that covers your processes, your standards, and how you’re going to monitor and improve over time. Your QMS should be aligned with your company’s goals and strategy.
3. Conduct a Gap Analysis
Before you can get started, you need to figure out where you stand. A gap analysis will help you understand your current practices and how they measure up to ISO 9001’s requirements. It’s like a health check-up for your business. What are you doing well? Where do you need to improve? Once you know where the gaps are, you can start addressing them.
4. Create and Implement New Processes
This is where the real work begins. Based on your gap analysis, you’ll need to implement new processes or adjust existing ones to meet formation iso 9001. This could mean developing new documentation, refining your workflows, or training staff on new procedures. It’s all about improving the consistency and quality of your work.
5. Internal Audits and Review
Once the processes are in place, it’s time for an internal audit. This is a chance to review how well you’ve implemented ISO 9001’s requirements and check whether the processes are working as they should. If any problems arise, don’t worry—it’s normal. The key is to identify them early, fix them, and keep moving forward.
6. Get Certified
After everything is in place and you’ve conducted your internal audits, it’s time to bring in an external auditor. They’ll assess your processes, check your documentation, and determine whether your business meets ISO 9001’s requirements. If everything checks out, congratulations—you’ll receive your certification.
7. Keep Improving
Once you’re certified, don’t stop! ISO 9001 isn’t a one-time achievement; it’s a commitment to continuous improvement. Regularly review your processes, set new goals, and always strive for better outcomes. That’s the beauty of ISO 9001—it’s designed to help you evolve and get better year after year.
The Benefits Beyond Certification: Why Continuous Improvement Matters
Okay, so now you have your certification. But why is continuous improvement such a big deal? Why should you care about always looking for ways to improve, even once you’ve “made it”?
1. Never Settling for “Good Enough”
In business, complacency can be dangerous. If you’re not actively looking for ways to improve, you’re falling behind. Customers’ expectations are always changing, new technologies are always emerging, and competition is always looking for a way to edge you out. Continuous improvement ensures that you’re always ahead of the curve, striving to do better every day.
2. Boosting Employee Morale
When employees see that the company is actively investing in improving its processes, it boosts morale. People want to be part of an organization that’s growing, learning, and making positive changes. And the best part? Involving employees in the improvement process helps create a culture of engagement, where everyone feels like they’re contributing to the company’s success.
3. Adapting to Change
The world changes fast—especially in today’s business environment. Being committed to continuous improvement helps you adapt. Whether it’s responding to customer feedback, changing market conditions, or new regulatory requirements, continuous improvement helps your organization stay flexible and responsive.
Key Challenges in Implementing ISO 9001 and How to Overcome Them
As with any significant change, implementing ISO 9001 comes with its challenges. Here are some common obstacles and how you can overcome them:
1. Resistance to Change
It’s human nature to resist change, especially when it comes to well-established processes. To overcome this, focus on communicating the benefits of ISO 9001 across your organization. Highlight how it will make everyone’s jobs easier, reduce stress, and ultimately help the company succeed. And don’t forget to involve your employees in the process—they’ll be more likely to embrace the change if they feel included.
2. Insufficient Resources
ISO 9001 implementation can take time, effort, and resources. If your team is already stretched thin, consider bringing in an external consultant who can guide you through the process. Sometimes, investing in expert help upfront can save you time and money in the long run.
3. Lack of Consistency
Consistency is key when it comes to maintaining your QMS. Make sure to regularly monitor and review your processes to ensure that improvements are sustained over time. Don’t let the momentum slip. Keep everyone involved, and ensure that quality is a priority in every decision.
Conclusion: The Road to a Better, More Efficient Future
ISO 9001 isn’t just a certification—it’s a mindset, a commitment to constantly improve and provide the best possible service to your customers. It’s about setting up processes that help your business thrive, ensuring that everyone is aligned with the company’s goals, and that your products and services consistently meet the highest standards.
If you’re ready to elevate your business and make continuous improvement part of your culture, ISO 9001 is a powerful tool that can guide you on that journey. It’s time to stop wondering and start improving. Your future self will thank you.
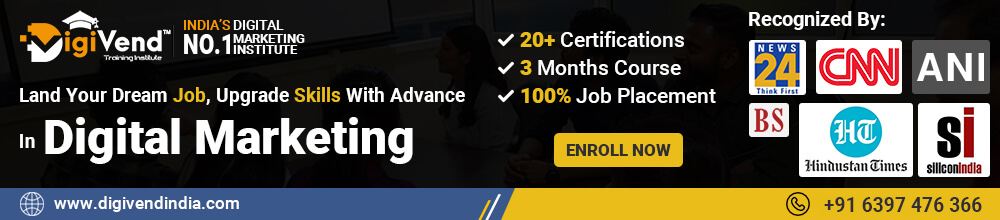