Choosing the Right Plug Valve for Your Industry: A Buyer’s Guide

When it comes to controlling the flow of fluids and gases in industrial systems, plug valves are a common and reliable choice. Their simple design, quick operation, and durability make them ideal for a range of industries including oil and gas, chemical processing, power generation, and water treatment. However, selecting the right plug valve for your specific application requires more than just picking the first available option. Understanding the different types, materials, functions, and configurations is essential to ensure long-term performance and operational safety.
This buyer’s guide provides essential insights to help you select the right plug valve based on your industry needs.
What is a Plug Valve?
A plug valve is a quarter-turn valve that uses a cylindrical or conically-tapered plug to control flow. The plug has one or more hollow passageways running through it that allow fluid to pass through when aligned with the pipe. When the plug is turned, the passage is closed off, halting the flow.
These valves are favored for their tight shut-off capability, simple operation, and minimal maintenance requirements. Plug valves are commonly used for on-off and sometimes throttling services in a variety of systems.
Key Features and Advantages
Before diving into selection, it’s helpful to understand the core advantages of using plug valves in industrial settings:
-
Quick Operation: A 90-degree turn fully opens or closes the valve, making them easy and fast to operate.
-
Leak-Tight Shutoff: Excellent sealing capabilities reduce the risk of leakage.
-
Compact Design: Plug valves are typically smaller and lighter than other valve types with the same pressure rating.
-
Durability: They are highly resistant to wear and corrosion, especially when made from robust materials.
-
Versatility: Available in various configurations and sizes to suit different industries.
Types of Plug Valves
Choosing the right plug valve depends heavily on the type most suitable for your application. Here are the main categories:
1. Lubricated Plug Valves
These valves use a lubricant injected under pressure between the plug and the valve body. The lubricant reduces friction and creates a seal. Ideal for high-pressure and high-temperature applications, they are commonly used in gas and oil pipelines.
2. Non-Lubricated Plug Valves
Instead of a lubricant, these valves use a sleeve or liner, typically made of PTFE or similar materials, to reduce friction. They are preferred for applications where contamination must be avoided, such as food processing or chemical industries.
3. Eccentric Plug Valves
These valves feature an eccentric (offset) plug that moves in and out of the seat during operation, minimizing wear and providing tight shutoff. They are particularly effective in wastewater treatment and slurry applications.
4. Expanding Plug Valves
Used in applications requiring double block and bleed capabilities, expanding plug valves provide a tight mechanical seal on both ends. They are typically used in critical systems where safety and zero leakage are crucial.
Factors to Consider When Selecting a Plug Valve
To ensure you choose the right plug valve, consider the following factors:
1. Media Type
Understand the type of fluid or gas the valve will control. Some media may be corrosive or abrasive, requiring special materials like stainless steel or nickel alloys for long-term reliability.
2. Pressure and Temperature Ratings
Check the system’s operating pressure and temperature. Lubricated plug valves are better suited for high-pressure applications, while non-lubricated types are more appropriate for moderate conditions.
3. Flow Control Requirements
If the application demands precise control or throttling, certain plug valve designs with specific port shapes (such as rectangular or diamond) are better suited to the task.
4. Material Compatibility
Choose valve body and plug materials compatible with the fluid. Common materials include cast iron, carbon steel, stainless steel, bronze, and various polymers for linings.
5. Maintenance Needs
Consider how often the valve will need to be serviced. Lubricated valves may require regular maintenance to replenish lubricant, while non-lubricated types generally require less upkeep.
6. Size and End Connections
Ensure the valve size fits your pipeline and that the end connections (flanged, threaded, welded) are compatible with your system.
Common Industry Applications
Each industry has unique requirements, and the role of the plug valve may differ accordingly:
-
Oil & Gas: Lubricated plug valves are widely used in upstream and midstream operations for their high pressure resistance and sealing strength.
-
Chemical Plants: Non-lubricated valves with corrosion-resistant linings are essential to handle aggressive chemicals.
-
Water Treatment: Eccentric plug valves are used for handling sludge, wastewater, and raw water with suspended solids.
-
Power Generation: High-performance plug valves are employed in steam and high-temperature water systems.
-
Pharmaceutical & Food Processing: Non-lubricated valves with sanitary designs are favored to maintain cleanliness and prevent contamination.
Installation and Operation Tips
-
Ensure the plug valve is properly aligned and supported to avoid stress on the pipe connections.
-
Periodically check for signs of wear, especially in abrasive or corrosive service conditions.
-
Follow the manufacturer’s guidelines for torque requirements to avoid over-tightening or damaging components.
-
Always confirm that the valve material and pressure ratings match your system specifications before installation.
Final Thoughts
Selecting the right plug valve is not just a matter of preference but a decision that directly affects the safety, efficiency, and longevity of your industrial system. By understanding the different types of plug valves, the specific needs of your industry, and the operational conditions of your system, you can make an informed choice that delivers reliable performance for years.
Whether you are updating an existing pipeline or setting up a new processing unit, invest time in assessing your requirements. With the right plug valve in place, you ensure smoother operations, reduced maintenance, and enhanced system integrity.
Also, read Ball Valve Explained: Key Features, Types, and Industrial Uses
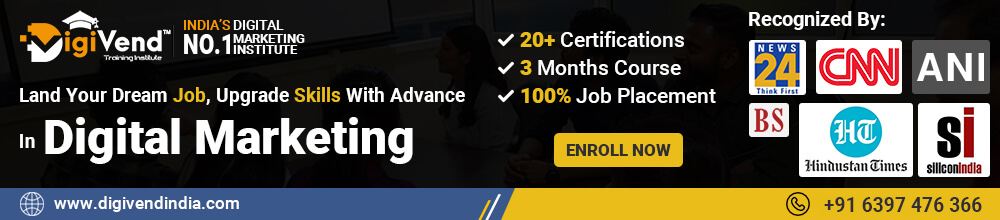