Why Construction Companies Are Turning to Software for Equipment Care
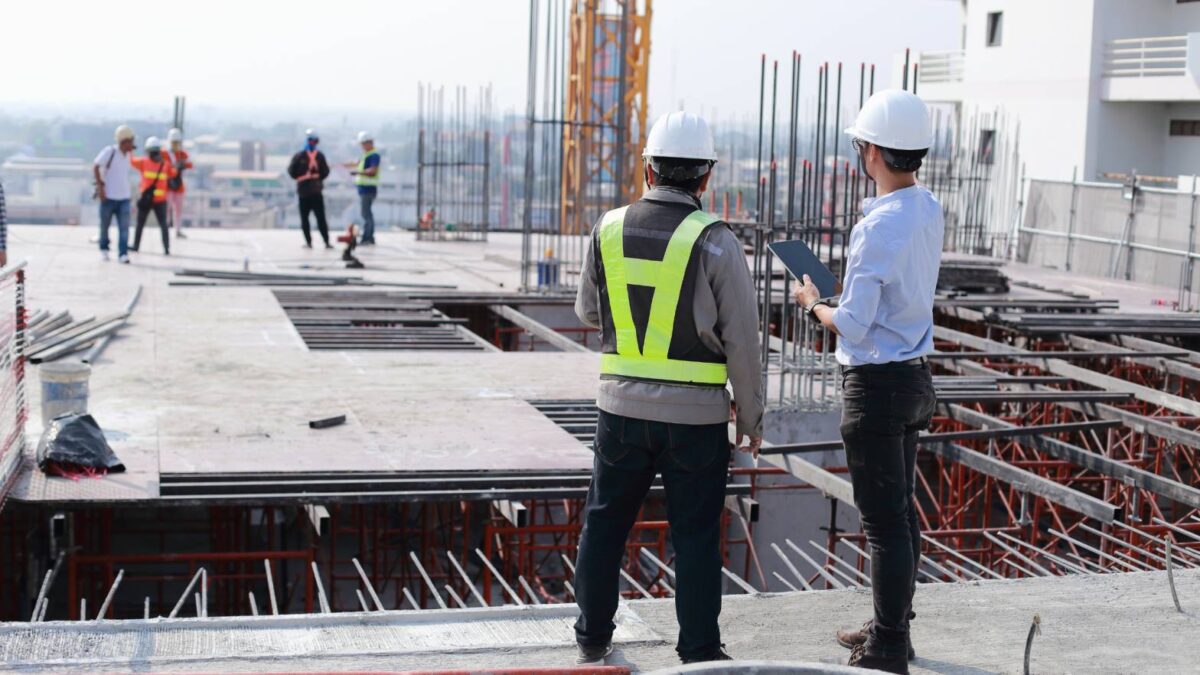
The construction industry is built on the backbone of heavy machinery, which is essential for completing projects on time and within budget. From cranes and bulldozers to excavators and mixers, these machines are integral to operations. However, maintaining this equipment is a major challenge for construction companies.
Unscheduled breakdowns, expensive repairs, and operational delays can seriously impact productivity and profitability. That’s why more and more construction companies are turning to digital solutions, particularly construction equipment maintenance software, to ensure their equipment stays in optimal condition and minimizes downtime.
In this article, we will explore why digital solutions are the future of equipment care and how equipment maintenance software is transforming the way construction companies manage their fleets.
The Challenges of Equipment Maintenance in Construction
Construction projects rely on equipment that must be reliable and efficient to meet tight deadlines and stay on budget. However, managing a fleet of machinery across multiple job sites can be overwhelming.
Traditional methods of equipment maintenance, such as paper logs, manual tracking, and on-site inspections, can be inefficient and error-prone.
Without a proper system in place, construction companies often face challenges such as:
- Unpredictable breakdowns: Equipment that hasn’t been properly maintained can suddenly fail, causing project delays.
- High repair costs: Emergency repairs tend to be far more expensive than preventive maintenance.
- Downtime: Machinery that is down for repairs can halt work, which delays project timelines and increases costs.
With equipment maintenance software, these challenges can be mitigated by streamlining maintenance schedules, improving equipment monitoring, and ensuring that machinery stays in optimal working condition.
Why Construction Companies Are Embracing Software Solutions
1. Automated Preventive Maintenance
One of the key benefits of equipment maintenance software is its ability to automate preventive maintenance. In traditional maintenance systems, companies often rely on scheduled inspections or manual logs to track when equipment needs maintenance. However, these systems are prone to errors, and it’s easy for maintenance tasks to be missed or delayed.
Digital solutions, on the other hand, automate the maintenance process by generating alerts based on machine hours, manufacturer recommendations, or predefined intervals.
The software can notify fleet managers when equipment requires service, such as oil changes, tire replacements, or brake inspections.
By staying on top of routine maintenance, construction companies can prevent minor issues from escalating into expensive repairs, ensuring that machinery is always ready to perform.
For example, construction equipment maintenance software can automatically send alerts for routine oil changes when a machine hits a certain number of operating hours, reducing the risk of equipment failure due to neglect.
2. Real-Time Monitoring and Data Collection
With the integration of sensors and telematics,equipment maintenance software allows for real-time monitoring of machine performance.
By tracking critical data, such as fuel consumption, engine temperature, tire pressure, and operating hours, construction companies can detect early signs of mechanical issues.
For instance, if the software detects that a machine is operating at an unusually high temperature, it can trigger an alert to the maintenance team.
This early warning system helps prevent major breakdowns and costly repairs by enabling construction companies to address issues before they become critical.
Real-time data also allows fleet managers to keep a closer eye on the condition of the machinery, ensuring that it is being used efficiently and safely.
By making data-driven decisions, construction companies can improve equipment performance, reduce fuel consumption, and extend the lifespan of their machines.
3. Improved Efficiency and Reduced Downtime
Unscheduled downtime due to equipment breakdowns can be costly for construction companies, as it halts work and delays project timelines.
Equipment maintenance software helps minimize downtime by providing fleet managers with insights into when equipment is due for maintenance, allowing them to schedule repairs or inspections before breakdowns occur.
Additionally, by tracking machine usage and performance in real-time, businesses can identify underutilized equipment and move it to sites where it is needed most, ensuring that all equipment is being used efficiently.
This increases the overall efficiency of the fleet and reduces unnecessary rental costs or equipment purchases.
By preventing breakdowns, reducing unplanned downtime, and optimizing equipment usage, construction companies can keep projects running smoothly, avoid delays, and reduce the overall costs of their operations.
4. Cost Savings on Repairs and Maintenance
One of the most compelling reasons construction companies are adopting equipment maintenance software is the cost savings associated with preventive maintenance.
Emergency repairs are often significantly more expensive than routine maintenance. In fact, studies show that companies can save as much as 40% on maintenance costs by adopting a preventive maintenance strategy.
By automating maintenance schedules and using real-time data to monitor equipment health, construction companies can detect small issues before they become major problems.
This proactive approach helps to avoid costly repairs, emergency fixes, and replacements. In addition to saving money on repairs, equipment maintenance software also helps businesses reduce operational costs by improving fuel efficiency and equipment utilization.
5. Compliance and Reporting Made Easy
For construction companies, maintaining compliance with regulatory standards and industry requirements is essential.
Equipment maintenance software helps companies stay compliant by keeping detailed records of all maintenance activities. These records can be accessed at any time and used for audits or inspections.
The software also ensures that equipment is inspected regularly and meets safety standards. Many regulatory bodies require businesses to keep records of maintenance, inspections, and repairs.
With equipment maintenance software, all these records are automatically logged, creating a digital audit trail that is easy to review and report when necessary.
The Future of Construction Equipment Maintenance Software
As technology continues to evolve, equipment maintenance software will continue to improve. The integration of artificial intelligence (AI) and machine learning will further enhance the predictive capabilities of these systems, enabling businesses to forecast potential issues with even greater accuracy.
In the near future, we can expect equipment maintenance software to integrate seamlessly with other aspects of fleet management, such as inventory control, procurement, and asset tracking, creating a fully integrated solution for managing construction operations.
The future of maintenance management will be even more automated, predictive, and data-driven, ensuring that construction companies can operate at peak efficiency.
Conclusion
As construction companies face increasing pressure to deliver projects on time and within budget, adopting construction equipment maintenance software is a strategic move toward improving operational efficiency, reducing downtime, and cutting maintenance costs.
By automating maintenance schedules, providing real-time insights, and improving data-driven decision-making, digital solutions help businesses maximize the performance of their equipment and extend its lifespan.
For construction companies looking to stay competitive in an industry driven by technology, equipment maintenance software is a game-changer. It not only helps ensure that equipment runs smoothly but also contributes to greater profitability, improved safety, and enhanced productivity.
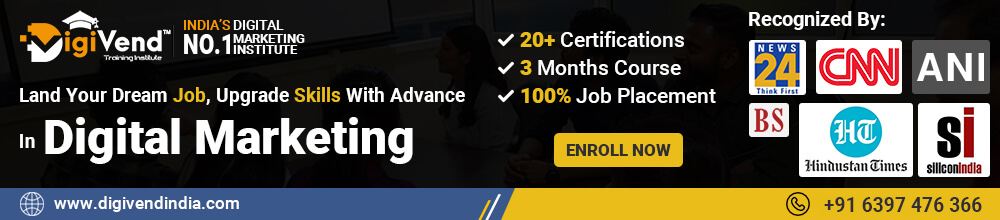