Top 10 Screen Printing Shirt Mistakes To Avoid

Are you worn out with inefficient Screen Printing Shirt designs? You may be a complete novice or a seasoned expert, it is likely that you have faced some printing process errors before. These mistakes can extract a hefty price in terms of time, money, and resources. But don’t worry! With the right understanding of the most common issues and blunders, you can ensure success in every Screen Printing Perth project. Small mistakes such as ink consistency and designs being off center can bring powerful negative impacts. You just need to keep your creative juices flowing and do not let miscalculations get the best of you.
In this article, we describe the most common problems that come with Screen Printing Shirts and outline the most effective strategies for avoiding them. Blurry prints, distorted designs, ruined shirts, crooked prints are simply a few of the many obstacles you will no longer face. The idea of achieving professional quality prints will no longer be out of reach. Now, if you are keen on taking your screen printing skills to the next level, let’s jump straight forward into practical ways of achieving impeccable results.
Having the Wrong Fabric for the Shirt
One of the detrimental errors one can make while screen printing shirts is selecting the fabric of the shirt. The fabric is a major factor in the success of the design. Some fabrics do not soak the ink well and some will prematurely crack or fade the design.
The ideal fabric for Screen Printing Shirts is 100% cotton. Cotton shirts will take in the most ink, which guarantees that your design will be bright and durable. In addition, it feels nice and soft on the body, perfect for custom shirts. Do not use poor-quality materials such as polyester or blends for intricate designs because the prints will look awful. In such cases, fabric becomes non absorbent causing the design to fade or be incomplete.
Things to Note:
- Be sure to use 100% cotton shirt for vibrant and long lasting prints.
- If you have to use blended fabric, print it first to see if it sticks.
Skipping Steps While Preparing The Screen.
The accuracy of a Screen Printing Shirt job relies first on the screen preparation. If this step is ignored or done poorly, the results will be out of focus or off target. The screen must be cleaned, coated with emulsion and light exposed to it and the correct time must be done fully.
Screen Preparation that isn’t done properly can lead to the ink leaking through the mesh, leading to a muddled picture. And if there is no proper cleaning of the screen, there will be mixing of the fresh and used inks leading to colors blending in unappealing ways.
What You Need to Do.
- Prepare and clean your screens before the printing process begins and set the blank parameters for it.
- Loosen the dirt or old ink set into your screen mesh and make sure that the screen mesh is tight.
Not Being Mindful of the Amount of Ink Used.
While printing, it may be beneficial to the screen printer to add extra ink more readily for immerging prints, but this is one of the most common mistakes in screen printing. Bleeding, bogus ink smear printing and printed images that are too deep and thick are just some of the many reasons why having and using an excessive amount of ink is problematic.
Excess ink will either run or spread over the lines, thus ruining the sharpness of your artwork. Moreover, it makes the shirt uncomfortable to wear since the ink forms a thick layer that does not breath properly.
What to Do:
- Use the least possible amount of ink, and it on the screen as much as possible.
- Print on a scrap shirt before the final one to check if there is enough ink on the printer.
Not Testing the Design Before Printing
Printing without any prior testing of the design can put you at a huge financial loss. There are times when a design looks attractive on paper, but once printed on the Screen Printing Shirt, it does not turn out as planned. Alot of times, the print is misplaced, the colors are wrong, or the images get distorted.
Testing is imperative for ensuring any issues are fixed before a full order is completed. Many screen printers skip this step because they feel it takes too much time, but in reality, it will save you from wasting materials and time on unpleasant prints.
What to Do:
- As a rule of thumb, always print a test shirt before making the actual batch.
- Look out for design problems in the test print, such as misalignment or color changes, and fine tune them accordingly.
Overexposing the Screen
Imagine leaving your screen exposed for an extended period. This could burn an image which completely hinders the screen from functioning correctly and allows the ink to pass through the screen. The image produced will be obscured and overly dark, rendering the design confusing and vague. The overexposure will also cause mesh damage which will affect the screen’s quality in the long run. For this reason, it is important to consider the specific screen’s emulsion type and the corresponding recommended exposure time.
What to Do:
- Ensure that the exposure time is suitable for the type of emulsion and screen you are using.
- Check the image before and after the exposure to confirm that it is developing correctly.
Misaligning the Screens
This is arguably one of the most annoying aspects of screen printing. Misaligning your screens can prove to be a problem especially when trying to print multi-color designs. In the event that the screens are not aligned, the differing colors will be out of sync resulting in an unclear or blurry design. This is a critical error that has the potential to ruin your Screen Printing Shirt.
What to Do:
- Make use of a registration system when aligning screens to avoid misalignment.
- When working with several colors, confirm your screen alignment in order to save yourself from unnecessary hassle later on.
Failure to Cure Ink Properly
Curing refers to drying the ink on the shirt so that it does not come off. If you do not cure the ink correctly, then your design can crack or peel after a few washes. Different inks have different curing temperatures and times so it’s very important to follow the guidelines of the manufacturer.
Your design might appear dry when you finish it, but if the curing process is incomplete, reap and tear will make it impossible for the design to last.
What to Do:
- Always cure the ink based on the guidelines of the manufacturer.
- Ensure to test the curing process on a sample shirt first to see if the print will endure fading or cracking in the long run.
Using the Wrong Type of Ink
Not all inks are made similarly and if you pick the wrong one for the fabric you are using, it can lead to lackluster results. For instance, water-based inks work with cotton shirts, but for some reason they do not work at all with synthetic fabrics such as polyester. Using mismatched inks will mean that the design will either fade, crack, or fail to adhere to the fabric.
What To Do:
- Pick the right ink based on the fabric you’ll be using on your Screen Printing Shirt.
- Talk to your ink supplier to find out which ink works best for your project’s needs.
Not Remembering Fabric Shrinkage
The shrinkage of fabric is one of the areas that a lot of screen printers fail to incorporate, mainly with 100% cotton shirts. A shirt has a good chance of shrinking after it’s washed and dried and along with that sometimes the design gets distorted. This can make the print appear to be off-center or in some cases, stretched out which is not ideal.
What To Do:
- Factor in fabric shrinkage in the design along with printing processes.
- Prior to starting to print, pre wash the shirts to get rid of as much excess shrinkage as you can.
Not Washing Screens After Each Usage
If you do not wash your screens after every single use, the additional ink left on the screen can worsen the primary prints. This can cause unwanted lines or a sudden shift in color on the Screen Printing Shirt as the new colors blend with the residual ink.
What To Do:
- Make it a point to wash your screens after every use to get rid of as much ink residue as you can.
- When you’re done using the screens, store them properly to keep them clean and in good condition.
Conclusion
Perfect Your Screen Printing Technique Avoid Making These Top 10 Screen Printing Shampoo Mistakes Effective screen printing tips that can make your design come out as professional looking, clean, perfect and full of vibrant colors. If you take your time for choosing the right materials, screen preparation, testing your designs, and ensuring appropriate curing, you will be able to make prints that can stand the test of time.
Whether you’re printing a custom Screen Printing Shirt or looking to do a large order, these suggestions will help you prevent mistakes that may cost a fortune while improving your printing technique. Remember, the secret to achievement is having a plan, conducting tests, and practicing detail. Understanding gaps in your knowledge brings us to amazing flawless designs; now you just need to put in the work. Enjoy printing!
FAQs about Screen Printing Shirt
What is the common issue in screen printing?
Ink smudging or bleeding, which is the smearing or distortion of the design due to the lack of control over the spread of the ink, is one of the more common problems among screen printers. This typically happens when there is too much screen ink and there is lack of proper screen mesh preparation and thus results to the improper distribution of ink. The other major issue that stands sharing proper curing of the ink that allows the printed image to crack, fade or peel away all together. If the required heated temperature is not sustained for a suitable duration the ink is unlikely to bond well with the fabric and thus reduces the lifetime value on the print, so it remains undamaged for a longer period of time.
Misalignment, or poor registration, is another problem frequently encountered in screen printing. Colors in a multi-colored design do not mesh well together. This happens when the screens are set too fast, or when the screens are not set at the correct position. In addition, failing to clean the screens correctly after every use can result in excess ink and residue that make the next prints less precise. The screens getting dirty can also lead to poor quality prints due to dust or debris blocking the screens. These common problems can typically be resolved by using proper screen tension, ink viscosity, curing time, and environmental control.
What mistakes should you avoid when screen printing?
Setting up and preparing for screen printing is one area where you do not want to cut corners. Skipping steps, like selecting incorrect mesh counts, can be detrimental to the end product. Another classic mistake to avoid is inundating the screen with excessive ink. This often causes smudging or uneven applications which ruin most of the print. Furthermore, when pulling the squeegee, pressing down too hard, or doing so unevenly distorts the design. This is particularly troublesome with delicate artworks since they lose the beauty in the actual prints.
Another major no-no is the usage of conflicting inks for different kinds of fabric. Most inks are made for certain materials, so using them incorrectly will likely cause the fabric to bleed, crack, or have the print fade quickly. Moreover, not properly washing the screens can also create problems. Without cleaning, ink residue will build up and block crucial details of subsequent prints. In addition, overexposure to UV light and excessive emulsion usage will lead to thick or blurry prints. Sticking to appropriate screen printing guidelines and avoiding the above blunders, guarantees quality prints every time.
What type of T-shirt is best for screen printing?
Blended fabrics like the cotton polyester blend fall short compared to cotton when it comes to vibrancy and durability. While these materials do have their advantages, their level of vibrancy and durability does not compare to pure cotton. Limiting the amount of ink used during print for polyester will more often than not cause the prints to crack or fade, which is not the intended result. Heavier shirts are better suited for block prints while lighter compositions work better with detail and intricacy. It is important to regulatethe fabric’s texture and evenness, as uneven or rough fabric can distort the design’s print.
What Are 4 Disadvantages of Screen Printing?
As versatile and popular as screen printing may be, it surely does has disadvantages and flaws, such as cost effectiveness and time efficiency. High-set up cost is a prime example, especially for small runs. In comparison to printing, it requires the custom construction of each screen design which is both costly, not very efficient, and time consuming. For multi-colored designs, there exist multiple screens for each color, raising the cost and complexity.
Another limitation is the difficulty of printing high structure designs. A screen print is often incapable of capturing detailed and quaint features, especially when there is a lot of small text or detailed graphics. Compared to other printing techniques, there is a greater degree of ink diffusion with screen prints, and therefore, their images lack precision.
Another disadvantage of screen printing compared to other types like digital printing is that it is not as efficient, especially when printing in bulk. The amount of time needed for a print job is further increased by the drying time needed for each layer of ink, which can take a while. Screen printing also suffers from the inability to adequately reproduce designs that need subtle color changes or photographed images. Solid colors are used, which make it impossible to capture the details of photographs or transitions of colors seamlessly.
What is better than screen printing?
Although screen printing is popular, there are more useful methods out there for various printing purposes. One of them is Direct-to-Garment (DTG) printing, specially for detailed designs with many colors. Unlike screenprinting, which requires screens, a DTG printer applies ink directly onto the fabric, similar to how an inkjet printer works. Full color detailed prints can be achieved this way. It is perfect for T-shirts that need to be printed in small quantities and are more complicated, as well as those that make use of gradient colors. Moreover, the absence of screens means that DTG makes these types of orders much faster and cheaper to set up.
Heat transfer printing is a great option for custom designs where intricate details need to be included. This process involves heating up an image on a special paper so that the ink can be transferred to the fabric. Heat transfers work best on photographic images, small designs, or multi-colored intricate pieces. Although, prints created by heat transfer methods have lower durability compared to screen print methods and may fade or peel off after repeated washing. At the end of day, the decision of whether to use screen printing or alternatives like DTG or heat transfer printing comes down to the complexity of the design, how many shirts need to be printed, and how long the print needs to last.
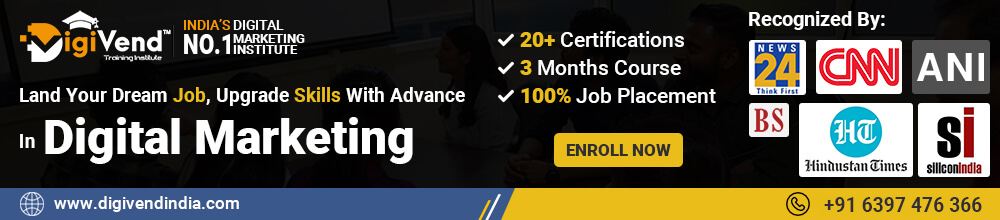